A Comprehensive Guide to the Refine and Advantages of Plastic Extrusion
In the substantial realm of manufacturing, plastic extrusion arises as a vital and highly reliable procedure. Translating raw plastic into constant accounts, it provides to a huge selection of markets with its impressive versatility.
Understanding the Basics of Plastic Extrusion
While it might show up complex at initial glance, the procedure of plastic extrusion is essentially straightforward - plastic extrusion. It is a high-volume production method in which raw plastic is melted and shaped right into a constant account. The procedure begins with the feeding of plastic product, in the type of pellets, powders, or granules, into a heated barrel. The plastic is after that melted using a mix of heat and shear, applied by a turning screw. Once the molten plastic gets to completion of the barrel, it is required with a small opening called a die, shaping it right into a desired type. The designed plastic is after that cooled, solidified, and reduced right into desired sizes, completing the procedure.
The Technical Refine of Plastic Extrusion Explained
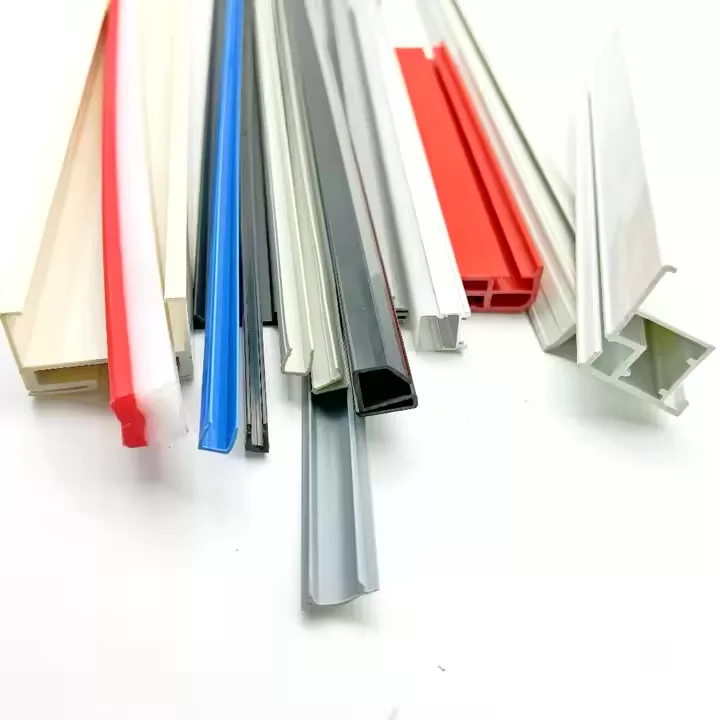
Sorts Of Plastic Suitable for Extrusion
The option of the right type of plastic is an essential element of the extrusion procedure. Different plastics use unique properties, making them more suited to specific applications. Polyethylene, for example, is generally used because of its inexpensive and very easy formability. It provides outstanding resistance to chemicals and dampness, making it perfect for products like tubing and containers. In a similar way, polypropylene is an additional preferred option due to its high melting factor and resistance to fatigue. For even more robust applications, polystyrene and PVC (polyvinyl chloride) are usually chosen for their stamina and toughness. Although these are typical choices, the choice ultimately relies on the certain needs of the item being generated. So, understanding these plastic kinds can significantly boost the extrusion procedure.
Comparing Plastic Extrusion to Other Plastic Forming Approaches
Understanding the sorts of plastic appropriate for extrusion leads the way for a more comprehensive conversation on just how plastic extrusion compares to other plastic creating methods. These include shot molding, blow molding, and thermoforming. Each technique has its special uses and benefits. Injection molding, as an example, is superb for developing intricate parts, while strike molding is perfect for hollow items like containers. Thermoforming excels at creating superficial or huge components. However, plastic extrusion is unequaled when it concerns producing continual profiles, such as seals, gaskets, and pipes. It also allows for a regular cross-section along the size of the product. Thus, the choice of method mainly relies on the end-product demands and specifications.
Trick Advantages of Plastic Extrusion in Production
In the world of manufacturing, plastic extrusion provides numerous considerable advantages. One significant advantage is the cost-effectiveness of the procedure, which makes it a financially appealing production technique. Furthermore, this technique supplies exceptional item flexibility and boosted production rate, thus boosting general manufacturing efficiency.
Cost-efficient Manufacturing Technique
Plastic extrusion leaps to the center as a cost-efficient manufacturing method in manufacturing. This process stands out for its ability to produce high volumes of product swiftly and effectively, offering producers with considerable cost savings. The primary cost advantage is the capability to make use of much less expensive raw products. Extrusion utilizes polycarbonate materials, which are less expensive contrasted to ceramics or steels. Additionally, the extrusion process itself is relatively straightforward, minimizing labor prices. In addition, plastic extrusion needs much less energy than conventional production techniques, adding to reduced functional costs. The process likewise decreases waste, as any faulty or excess materials can be recycled and recycled, giving an additional layer of cost-effectiveness. On the whole, the economic advantages make plastic extrusion a very appealing choice in the production industry.
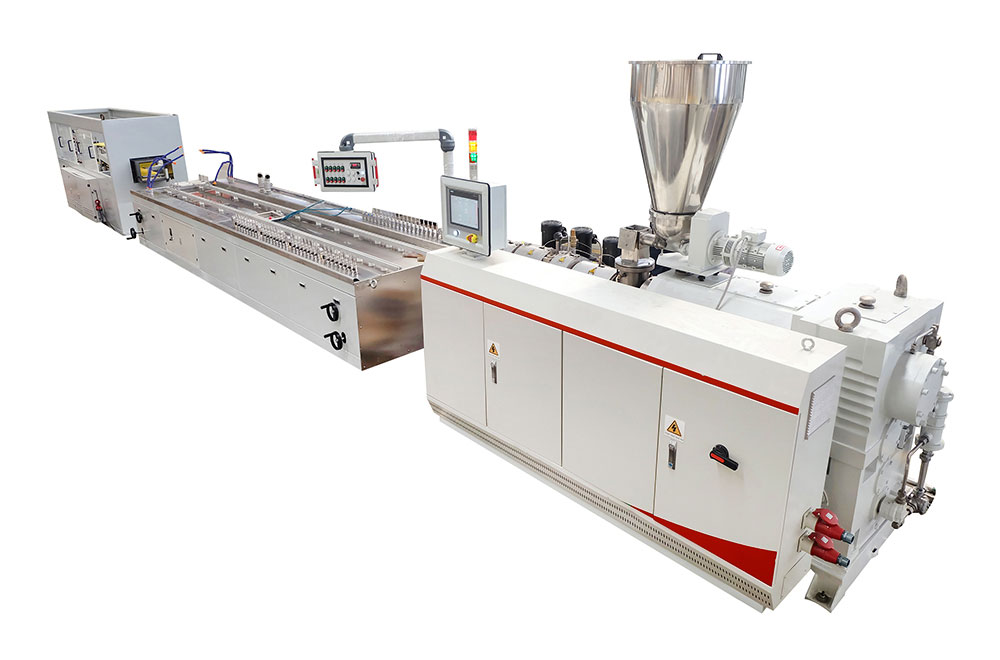
Superior Product Adaptability
Beyond the cost-effectiveness of plastic extrusion, one more substantial advantage in producing hinge on its superior product flexibility. This process permits the development of a wide array of items with varying designs, forms, and dimensions, from simple plastic sheets to complex profiles. The flexibility is attributed to the extrusion die, which can be personalized to generate the preferred item style. This makes plastic extrusion an excellent option for industries that call for personalized plastic parts, such as automotive, building, and product packaging. The capability to produce diverse products is not only beneficial in conference specific market needs yet also in allowing manufacturers to explore new line of product with minimal capital expense. Essentially, plastic extrusion's product flexibility cultivates innovation while boosting functional efficiency.
Improved Production Speed
A considerable advantage of plastic extrusion exists in its improved production speed. Few various other manufacturing processes can match the rate of plastic extrusion. Additionally, the ability to maintain regular high-speed production without sacrificing product top quality sets plastic extrusion apart from other approaches.
Real-world Applications and Impacts of Plastic Extrusion
In the world of production, the method of plastic extrusion holds extensive value. The financial benefit of plastic extrusion, mostly its affordable and high-volume outcome, has revolutionized production. The sector is constantly striving for developments in recyclable Visit Website and naturally degradable materials, suggesting a future where the benefits of plastic extrusion can be preserved without compromising ecological sustainability.
Final thought
In conclusion, plastic extrusion is a highly efficient and effective approach of changing basic materials right into diverse items. It uses countless advantages over various other plastic developing read review methods, consisting of cost-effectiveness, high outcome, marginal waste, and layout adaptability. Its influence is greatly felt in various industries such as building and construction, automobile, and durable goods, making it a critical process in today's manufacturing landscape.
Delving deeper into the technical procedure of plastic extrusion, it begins with the selection of the appropriate plastic product. When cooled, the plastic is reduced into the needed lengths or injury onto reels if the product is a plastic film or sheet - plastic extrusion. Contrasting Plastic Extrusion to Other Plastic Forming Techniques
Recognizing the kinds of plastic suitable for extrusion paves the method basics for a broader conversation on exactly how plastic extrusion stacks up versus various other plastic creating techniques. Couple of other manufacturing processes can match the speed of plastic extrusion.